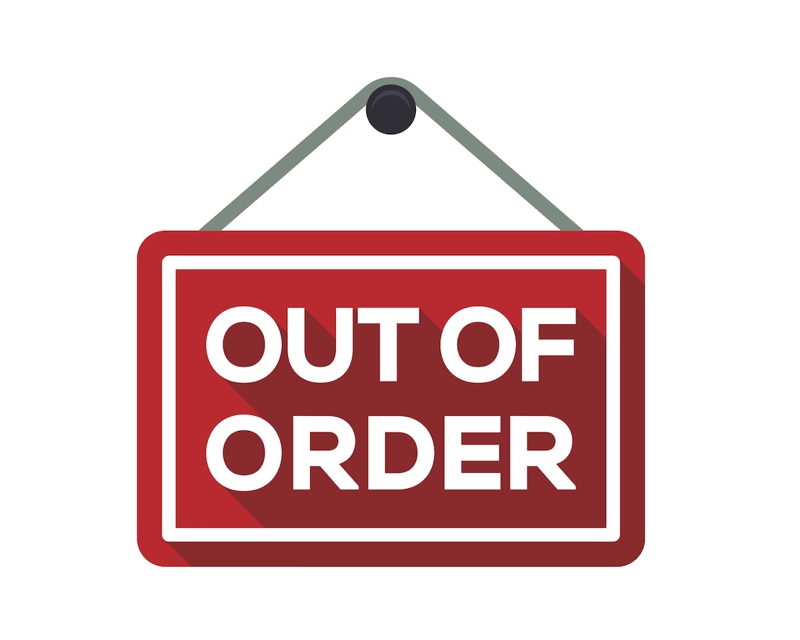
Three major factors require airport operators to constantly examine and optimize their technical departments for continued operational success:
- New and tightening regulatory and environmental requirements drive the technical complexity of buildings, facilities and plants as well as the difficulty of their operation\n
- Competition for returning traffic is fierce among airports, due to substantial overcapacity. Thus, customer experience will become a key differentiator\n
- Continued introduction of ever-advancing technologies will increase expectations, purpose and objectives within the organization. It is therefore crucial to keep a finger on the pulse of technological developments and remain ahead of the curve
Efficient Technical Control Centers are a success factor in operating an airport
In this article we show why you should tackle these challenges at your technical control center and provide three major levers to lead your optimization project to success.
How Technical Control Centers are impacting airport operations
Technical Control Centers may not be the first thing that comes to mind when thinking of integral parts of operating an airport, but they play a vital role behind the scenes. They sit at the fulcrum of incident response and technical services and thus determine both customer satisfaction and the response effectiveness.
Perceived quality of an airport’s infrastructure will prove a notable differentiation factor in a weak demand environment that has airports vying for traffic volumes to return. This perception is materially influenced by the ability of the airports technical maintenance capability to swiftly repair faulty facilities and fix malfunctions – best case even before a passenger recognizes it. In this context, staff in the Technical Control Center are the facility management organization’s face to the customer, be it the operational departments, airlines, commercial tenants and ultimately the passenger.
Equally important, the initial reaction of TCC staff to a report determines the effectiveness of the facility management department’s response and, in turn, its cost. This is due to the nature of a TCC agent’s role as a communications interface. When an issue is first reported, they must identify and extract all relevant information in order to make a qualified decision to pass on the right team, engineer or expert to pass it on to, along with the most appropriate action required, as well as the issue’s priority. A correct initial judgement by a TCC agent can thus substantially save time and effort all along the process throughout the whole facility services department. Of course, a number of faults will seem mundane and can easily be fixed (think: “have your tried turning it off and on again?”). Others, however, will be much more critical in terms of the parties or processes affected and the urgency they need to be investigated and solved. The key to maximizing added value is to automate the handling of everyday issues and focus on complex and difficult cases individually.est types available and assessed the advantages and disadvantages for different testing methods.
Moments of actual crisis are a third example for the important role Technical Control Centers can play. Be it a child stuck in an elevator or a complete breakdown of the baggage sortation system, low reaction times are key to salvage situations before they spin out of control. In such instances, pressure on the entire system rises exponentially, quickly exposing any interfaces or processes that are not up to standard. Airports’ Technical Control Centers can then demonstrate whether they are a solution driver or the weakest link in the response chain.
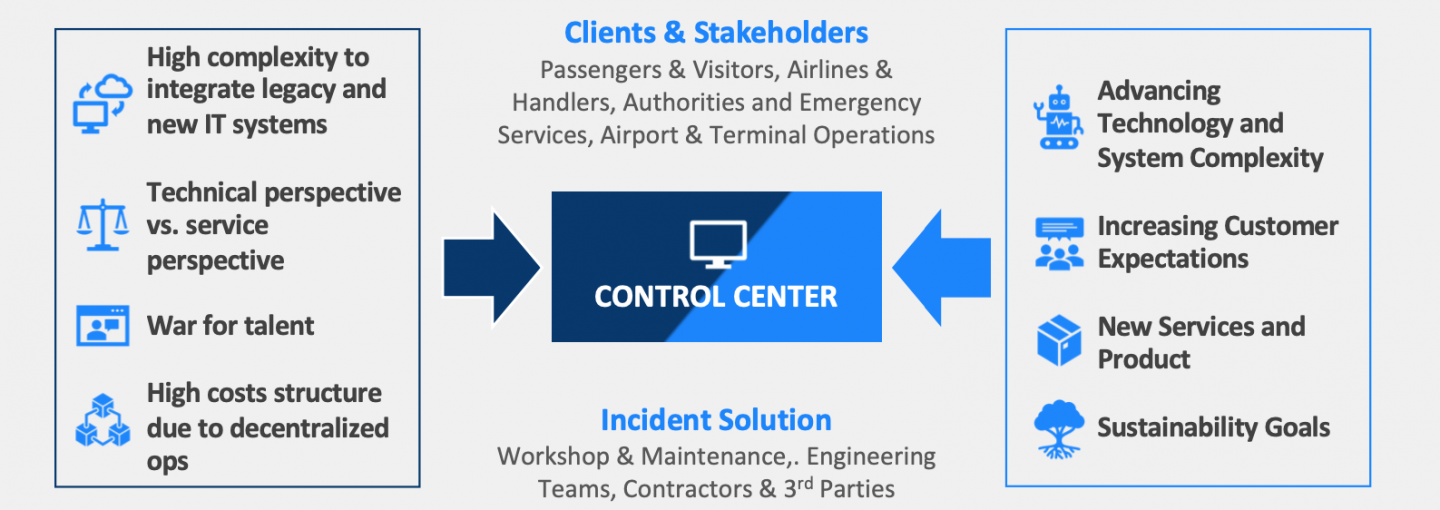
M2P’s view: drivers of complexity and fields of action
Working closely together with our clients, we have experienced certain reoccurring themes driving or impacting the effectiveness of technical control centers. Below we have outlined those we find most important.
Control centers are in an integral position to the entire incident management process. Yet, it often seems that management’s view is rather isolated, i.e. not capturing the full picture: Is the control center seen as an isolated cost center or is it possible to actually determine cost and value contribution along the entire process?
While tracking the Center’s direct staff or IT costs is fairly straight forward, getting an end-to-end view on total cost of maintenance is significantly harder to obtain. In most cases this would, however, lead to improved decision making.
Take the example of the Agents’ intra-day decision-making and evaluation of criticality: an isolated perspective naturally fosters short decision-making on a first-come-first-serve basis. With a better understanding of associated downstream costs along the process, repair jobs could be combined to help increase the effectiveness of teams on ground.
Isolated management views result in poor incentives for Control Center Optimization
Similarly, demand patterns are often insufficiently known or at least considered. Indeed, a good share of incidents coming in via the various channels (phone, email, BMS systems) is random. A more thorough analysis might, however, reveal certain patterns across weekdays, daytimes and seasons. Contrary to that is the Center’s shift plan which is often based on a more rigid regime. This might lead to structural idle time being left untapped or – even worse – fundamental understaffing during critical peaks. The consequence of taking isolated views on interdependent issues are inappropriate incentives for optimization of the Control Center. This prevents necessary investments in the function, as consequences benefiting the whole department further down the process chain are not taken into account.
Operational inefficiencies and outdated or unaligned tools
Enabling staff to perform to the best of their abilities and maximum efficiency depends in part on the systems supporting their work.
Historically driven, Control Centers often include a range of systems in use: Different buildings run on various Building Management Systems (BMS), protocol and communication systems have been added over the years. In this context, integration is often considered cumbersome and expensive. On top of this, constantly increasing requirements lead to further expansions to the IT portfolio, adding more complexity. In such heterogenous system landscapes, automation is hard to achieve. The resulting manual tranfer of data between systems provokes mistakes, while a lacking or incomplete integration of BMS prevents staff from effective system surveillance.
Another decisive contributor to performance is the effective organization of procedures and processes within the Control Center. On this front we have mostly observed a very generalist approach, with a broad range of topics and systems being covered by all agents. Irrespective of individual’s skill and knowledge, both decrease motivation as some agents find specialist tasks daunting and others’ expertise is “wasted” performing repetitive tasks. In addition, tasks are predominantly fulfilled manually, and on a case-by-case basis, revealing how a lack of automation is slowing down processes and creating extra procedural steps.
Even though technical equipment and support is of the essence, it eventually comes down to the people and the purpose they find in their jobs. Staff in control centers are regularly met with a variety of different expectations. Customers or passengers expect a maximum of service quality: both in terms of friendliness as well as the agent’s ability to identfy and solve problems and give appropriate feedback. On the other hand they require broad technical expertise and analytical skills to properly manage and maintain the technical systems.
Given their professional background and daily routine, employees in control centers often tend to have a culture of technical expertise, neglecting their impact on customer experience. Considering their position at the airport, it becomes evident why: control centers are often isolated from any operation, only having remote contact with customers and peer workers. This leads to a setting where agents do not recognize the value and impact of their work on the whole department and overall company. Eventually, they perceive a lack of definition regarding their roles, feeling a disconnect between their work and the value it provides overall.
People remain at the center of any successful change or improvement
It is thus up to senior and direct management to define a culture that balances service and technical orientation and makes sure the unit is properly represented within the entire nucleus of the airport. Culture and mindset should eventually follow the company’s overall strategic objectives: be it running on lowest cost or at highest service levels. By making clear whether the Technical Cntrol Center is to act primarily service-oriented or as a technical advisory function, senior managers set the scene not only for agent’s self-image, but also how the unit perceived by the entire company. Only if the Control Center is firmly embedded into the overall facility management strategy and has a clearly defined objective can its senior managers properly highlight its achievements to the wider company, rather than having to defend potential shortcomings or react to isolated requirements from stakeholders.
To leverage the full potential of Control Centers as an enabler for a nimble, cost-efficient and customer-centric maintenance organization, companies should seek a strategy to operations alignment. Concretely, this means that facility managers must be clear on what is expected from Control Centers, and how they fit into the overall maintenance organization. This includes strategic direction on service-orientation and technical priorities as well as streamlined processes and supporting tools.
Only if the Control Center is firmly embedded into the overall facility management strategy and has a clearly defined objective, will it be possible to fully leverage on the pivotal position of the control center.
Based on the this, we see three major levers to transform the control center to the next level:
Provide clarity on strategic objectives and the individual contribution
1. Next Level IT-to-Operations Integration
As in any industry, automation and digitalization are the key levers to drive performance improvement. In the context of control centers it is all about getting ahead of the demand curve: the less agents are occupied with reacting to incoming calls, the more they can focus on surveilling systems and predicting incidents before they become visible to the customer.
A seamless integration of IT systems and facility management processes is key to acheving this. AI driven systems are able to predict patterns and derive incident forecasts, thus reducing the amount of reactive intervention required from agents. Providing digital twins of facilities to agents will allow them to get better at identifying problems and dispatching technicians, in turn strongly increasing KPIs such as the first time fix rate. A full-fledged integration of systems – from the client to the workshop – will facilitate an efficient set-up of end-to-end processes and improved service delivery to the customer. Both will help support a necessary cultural shift in the self-image of Control Center staff – from someone manning a phone to a proactive steering of facility operations.
2. Reorganize Work Allocation and raise efficiencies
Given the range of tasks and spectrum of facilities overseen by a Control Center, it makes no sense to maintain a “one-size-fits-all approach to work allocation and simply have all agents perform the same duties. Instead, the Center’s processes can be split into recording and allocating reports on the front end, and decision-making on priorities and technical approaches on the back end. This increases efficiency by allowing staff to focus on critical and value-generating tasks, respectively, thus boosting morale and engagement as individual qualifications are factored in and acknowledged.
Ideally, splitting the tasks this way is based on a sound IT backbone supporting automation, report interpretation and allocation for further action. While such reorganization will certainly require a concerted change management effort, the eventually gained improvement in effectiveness will increase room to maneuver. The efficiencies gained can for instance be augmented by centralizing more functions into the center, increasing its service portfolio. Alternatively, certain functions could be combined into one center across various sites, greatly improving productivity.
3. Workforce Empowerment
People will remain at the center of any improvement. Similarly, the expecations and tasks of control centers will continue to rise, despite the current crisis. To better meet those expectations, it is essential to find a new approach towards hiring and developing the most suitable agents. With an increased split of tasks, it will be possible to move beyond developing everyone to the same level. Building upon individual strengths and preferences will instead strengthen the agents’ performance and help improve individual job-satisfaction. While experienced technical experts can focus on solving and managing complex technical issues, service professionals will be allowed to deliver a premium customer experience. This is completed by IT experts driving system integration and facility automation.
Conclusion
With the right approach, Airports can extract maximum value out of the technical control centers by focusing on IT-integration, competency-based work allocation and workforce empowerment. This ensures their Technical Control Center drives efficient facility management processes and enables a premium customer experience.
Click here for our related Control Center Optimization service.